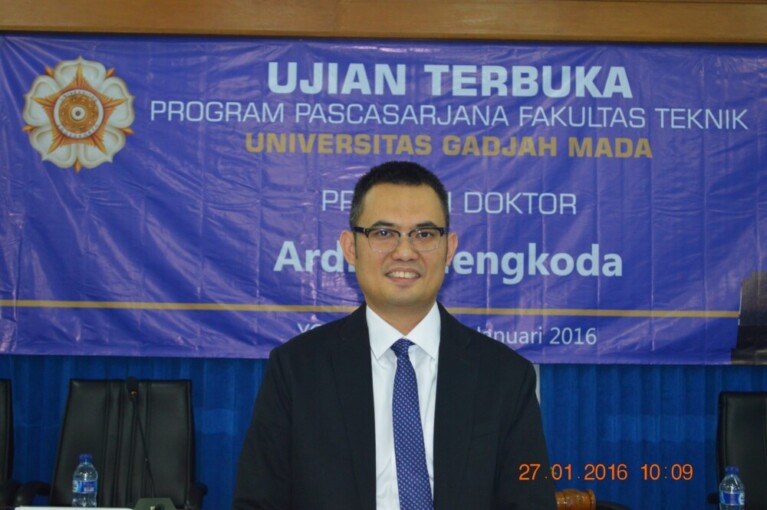
Based on the initial survey in 2004, Indonesia managed to locate potential reservoirs of methane hydrates for 850 (Tcf) in two main locations, namely the southern waters of Sumatra to the northwest of Java (625 Tcf) and in the Makassar Strait, Sulawesi (233.2 Tcf) . Given the high-risk operations, expensive and instability of gas at a normal pressure and temperature of sea surface, the challenge of methane hydrate offshore exploration and production becomes very large.
Unfortunately, until now there is no local or international regulatory standards on Integrated Safety Management System and Occupational Health and Risk-based Environmental Protection. Similarly, the risk of non-technical guidelines (NTR) is unavailable, either, as a reference for the exploration and production of methane hydrates.
That was stated by Ardian Nengkoda in the Auditorium of Faculty of Engineering of Universitas Gadjah Mada, Wednesday (27/1), at his open examination of doctoral program in chemical engineering. Accompanied by promoter, Ir. Supranto, M.Sc., Ph.D., and co-promoter, Prof. Ir. Suryo Purwono, MASC., Ph.D, and Imam Prasetyo, M. Eng., Ph.D., he defended his dissertation entitled Decision Making Support Tool for Selection of Methods in Methane Hydrate Production: A Case Study of Makassar Strait.
“The purpose of this study was to develop a tool to support decision making in the method selection of production of methane hydrate with case study of Makassar Strait of Indonesia,” Ardian Nengkoda said.
As the foundation methodology, Ardian describes workflow contains a new method that consists of a SWOT evaluation, HAZID analysis, quantitative assessment (laboratory tests or simulation modeling) and the estimated risk using Monte Carlo models, all processes are made in one integrated system. As bait, Knowledge Management (KM) and Process Flow Diagram (PFD) must be created and there are 6 scenarios of production methods, including thermal injection, depressurization, a combination of depressurization and injection of CO2.
“All will be evaluated in the study. The study shows a tool to support decision making (DMS) successfully and proved to able to choose the method of production of the most optimal, as well as meeting the level of minimum risk (ALARP) and proved to be capable of integrating HSE & RMS and NTR,” he explained.
Furthermore, the results of SWOT and HAZID evaluation concluded that the depressurization method is most feasible method of production. In addition, laboratory testing and modeling concluded that depressurization techniques require hydrate dissociation pressure of 100.75 psia, the critical pressure reached 778.23 psia and a critical temperature of about 78.99 degrees Celsius.
Ardian said that Monte Carlo model predicted all the risks of depressurization method shows the value of 5.88 with a probability of 90 percent, the average of 5.66 and standard deviation of 0.31 and are categorized as intermediate risk. Estimation of the overall risk is influenced by the indirect tendency of methane hydrate deposit reservoirs as much as 43% as well as the direct index and in situ.