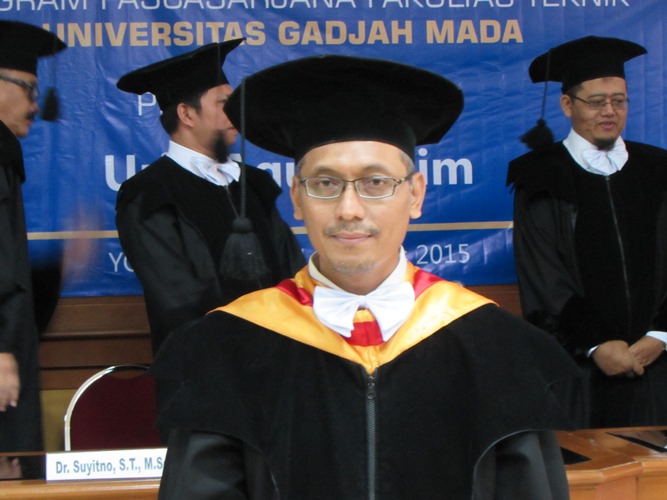
Kebutuhan implan tulang (osteosynthesis) dalam negeri meningkat seiring dengan jumlah korban patah tulang akibat bencana alam dan kecelakaan yang terjadi di Indonesia. Sayangnya, besarnya kebutuhan tersebut tidak diimbangi oleh ketersediaannya dan sejumlah besar implan tulang adalah barang impor. Salah satu jenis implan tulang yang banyak diaplikasikan pada pasien adalah dynamics compression pllate (DCP) karena DCP mempunyai bentuk sederhana dan sifat multiguna terutama untuk fiksasi tulang-tulang panjang seperti femur dan tibia.
“Namun, dalam aplikasinya sering dijumpai kasus kegagalan DCP sebagai pelat implan. Dan ini kasus penting di dunia ortopedi,”kata Urip Agus Salim pada ujian terbuka program pascasarjana Fakultas Teknik UGM, Jumat (21/8).
Urip menambahkan hampir semua dari pelat implan yang patah terjadi pada daerah lubang sekrup dan bahan pelat implan adalah baja AISI 316L. Di Indonesia memang belum ada data pasti tentang kejadian patah pelat implan, namun dari sudut pandang bahwa produk DCP berhubungan dengan keselamatan (kesehatan) manusia maka kasus kegagalan implan seharusnya tidak boleh terjadi.
“Kegagalan DCP yang terbuat dari baja AISI 316L ini jadi persoalan yang harus diupayakan penyelesaiannya,”papar dosen Jurusan Teknik mesin dan Industri, Fakultas Teknik UGM itu.
Dalam disertasinya berjudul Pengembangan Dynamics Compression Plate (DCP) Dengan Cold Working Untuk Penguatan Gliding Holes, Urip menjelaskan pembuatan produk DCP dalam negeri selama ini banyak melibatkan proses permesinan. Pembuatan bagian lubang gliding dengan pahat bentuk ball-nouse memerlukan waktu yang lama terutama set-up pahat dan biaya produksi tinggi (pahat mahal dan mudah aus). Penelitian yang dilakukannya untuk menginvestigasi perubahan sifat mekanik baja AISI 316L yang dideformasi plastis dengan teknik perluasan lubang.
“Hasil penelitian ini digunakan sebagai landasan untuk pengembangan produk nDCP dengan proses pembentukan,”katanya.
Hasil penelitian yang dilakukan Urip terlihat bahwa baja AISI 316L yang dideformasi plastis lokal dengan metode perbesaran lubang telah meningkat kekerasannya dari 150 VHN menjadi 200-450 VHN pada daerah sekitar permukaan lubangnya. Keberhasilan produksi DCP dengan proses pembentukan yang menggunakan sistem press-tool ini dipengaruhi oleh ukuran lubang pada bahan baku. Bentuk lubang yang perlu dipersiapkan adalah diameter lubang 5,5 mm dengan panjang lubang 11,4 mm untuk ketebalan pelat 3 mm dan 6 mm dengan panjang lubang 12,5 mm untuk ketebalan pelat 4 mm (Humas UGM/Satria)