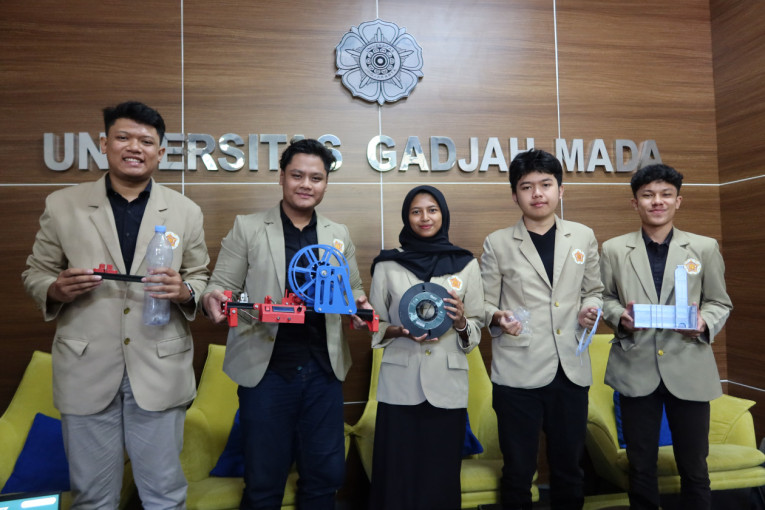
A Universitas Gadjah Mada (UGM) student team has introduced an innovative filament for 3d printing made from plastic bottle waste. The filament, named FilaPET, is claimed to have higher heat and tensile resistance and is more affordable than similar products. This innovation aims to reduce plastic bottle waste in Indonesia.
The team, consisting of five students, collaborated across their fields of study. They are Arifatus Sholihah (Faculty of Engineering), Azkal Anas Ilmawan (Faculty of Engineering), Kevin Deandra Septano (Faculty of Engineering), Afif Irfan Zein (Faculty of Engineering), and Maulana Iqbal Pambudi (Faculty of Animal Science).
Under the guidance of Dr. Nur Abdillah Siddiq, they developed FilaPET, a filament for 3D printing made from plastic bottle waste, as a creative and eco-friendly solution for the Student Creativity Program in Entrepreneurship (PKM-K) at UGM.
This innovative idea was conceived in response to the increasing plastic bottle waste. According to the Ministry of Environment and Forestry data, in 2022, Indonesia generated 68.5 million tons of waste and 11.6 million tons of plastic. This situation has put Indonesia in a state of emergency concerning plastic waste.
The team chose PET (Polyethylene Terephthalate) as the base material for FilaPET because PET is the primary material of plastic bottles, which is easy to recycle and has strong physical durability.
The creation of FilaPET is expected to reduce the accumulation of plastic waste in Indonesia. FilaPET can solve the urgent need for better plastic bottle waste management.
“Currently, the demand for 3D printing is quite high, with most consumers being students. Unfortunately, 3D printing filament is very expensive for students,” said Arifatus Sholihah, the team leader.
Therefore, FilaPET, priced at Rp52,500, can solve this problem. FilaPET costs around Rp300/gram, while other filament types are priced at Rp1,000/gram. This supports the demand for affordable 3D printing filament to produce various creations.
Azkal Ilmawan, the field production coordinator, added that this product’s advantage is its superior strength and durability compared to other existing products. FilaPET has a tensile strength of up to 55 MPa and heat resistance of up to 230°C.
Other specifications include an operational temperature setting in the 3D printer with a nozzle temperature of 240°C-260°C and a bed temperature range of 65°C-85°C.
Afif Zein, the group’s experimentalist, explained that the complexity of the production stages is not a major issue as it tends to be simple with the available equipment. The filament production process from used plastic bottles starts with collecting the bottles.
These bottles are then cleaned and sorted by type. After washing, the bottles are smoothed using heat sources such as a stove or heat gun. Next, the bottles are cut into long sheets using a fila-cutter. These plastic sheets are then processed in a filament maker machine, producing the final product.
The challenges they face include the product being relatively unfamiliar to the general public, affecting information dissemination and design. They will continue to introduce this innovation to garner response and interest from the public.
“Thanks to the enthusiasm and determination to be initiators in solving existing problems, we are proud that the product we have produced can be well received by the public and generate its appeal,” said Iqbal Pambudi, the media and information officer.
Kevin Septano, the marketing officer for FilaPET, added, “Our product’s pre-order is now open.” Currently, FilaPET can be purchased through marketplace platforms like Shopee. Further information about FilaPET can be found on social media platforms like Facebook, Instagram, X, TikTok, and YouTube.
Author: UGM FilaPET Team
Editor: Leony